V večini primerov tehnologije hitrega izdelovanja prototipov niso namenjene izdelavi funkcionalnih izdelkov, ampak le izdelavi oblikovnih prototipov bodočega izdelka ali maket v manjšem merilu, namenjenih preizkušanju. Vzemimo si primer podjetja, ki izdeluje mobilne telefone. Te običajno za predstavitve prihodnjih modelov teh še nimajo v proizvodnji, saj gre za konceptualne modele, ki naj bi prikazali oblikovne in funkcionalne smernice. Kdor je že hodil po sejmih, je imel možnost videti tako imenovane »dummy« izdelke prihodnosti, ki so običajno zaklenjeni v steklenih vitrinah. Jasno, saj so izdelani iz lesa, plastike, gline ali kaj vem česa še, in sploh ne delujejo. Namenjeni so predstavitvi zunanjega videza. A tudi izdelava takšnih modelov je lahko po klasični poti dokaj zamudna. Iz lesa jih je treba izrezljati, če pa so iz plastike, potrebujete orodje za vlivanje plastike, katerega izdelava ni samo zamudna, temveč tudi draga.
In tu lahko nastopijo sodobne tehnologije. Njihova prednost je v tem, da želeni izdelek narišemo znotraj grafičnega orodja za tridimenzionalno grafiko, izdelavo prototipa pa prepustimo napravi, ki ga lahko izdela v nekaj urah. In to takšnega, kot je bil ustvarjen »na papirju«. Seveda takšne naprave stanejo kar nekaj denarja, tako da je tudi prototip, narejen z njihovo pomočjo, lahko nesramno drag, vendar so stroški izdelave zgolj nekaj izdelkov kljub vsemu cenejši, kot bi bili, če bi ga izdelali po kakšni bolj klasični metodi. In tudi če je klasična pot cenejša, pa nikakor ni tako hitra – »zgolj« nekaj ur!
Potencialnih uporabnikov novih tehnologij izdelav prototipov je veliko, vedeti pa je treba, da so te naprave precej drage in da lahko le redka podjetja upravičijo stroške, povezane z njihovim nakupom in vzdrževanjem. Žal je pri večini novih tehnologij tako, da so na začetku prav nesramno drage. Res pa je, da lahko v pravem okolju pomenijo tudi konkurenčno prednost, kar ima vsekakor tudi svojo ceno. Če bi lahko industrijski oblikovalci svojim naročnikom prikazali maketo bodočega izdelka in hitro vnašali morebitne spremembe in popravke ali hitro naredili več konceptov izdelka, to zanje vsekakor pomeni konkurenčno prednost, ki lahko upraviči tudi morebitne večje stroške nabave takšne nove tehnologije.
Poleg hitrosti govori v prid tem napravam še marsikaj. Z njimi je komunikacija med partnerji učinkovitejša, saj je veliko nazornejše prikazati realen objekt kot njegovo bolj ali manj natančno prestavitev v računalniku ali na papirju, saj imamo ljudje zelo različne sposobnosti vizualizacije dvodimenzionalnega objekta. Hitrost izdelave tudi dopušča krajše čase od načrtovanja, preko odločanja do končnega izdelka. V tem delu pridejo do izraza lažje odpravljanje napak, hitrejša izvedba sprememb in možnost predstavitve več različic istega izdelka. In zakaj ne? Če bi bila tehnologija primerna tudi za domače uporabnike, bi ti morda lahko naredili tudi kaj za svoje domovanje. Kako najhitreje na primer do nove makete železnice?
STEREO LITOGRAFIJA (SLA)
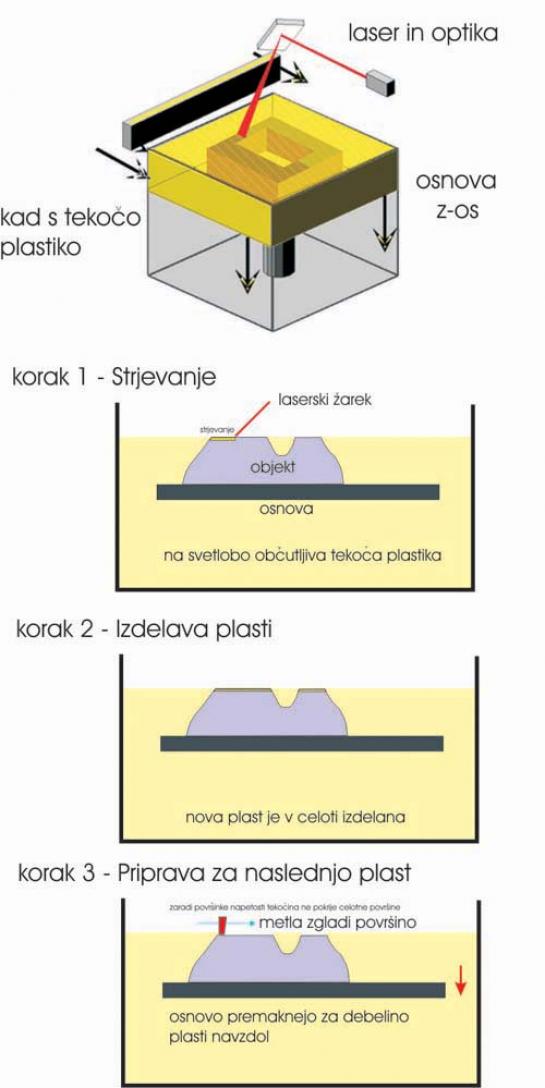
Pri tehnologiji stereo litografije gre za »strjevanje« na svetlobo občutljive tekoče plastike. Model nastaja plast za plastjo v koritu, napolnjenem s tekočo plastično maso. Računalnik krmili laserski žarek, ki deluje na ultravijoličnem delu svetlobnega spektra, ta pa povzroči, da se tekočina na obsevani površini strdi. Po zaključeni izdelavi ene plasti se nosilna osnova (platforma) nekoliko spusti, celotna površina se spet napolni s tekočini in korak se ponavlja, dokler ni izdelan ves objekt. Od debeline plasti in orientaciji objekta v kadi je odvisno, kako natančno bo le ta izdelan. Tipično je ena plast debela med 0,1 in 0,2 milimetra.
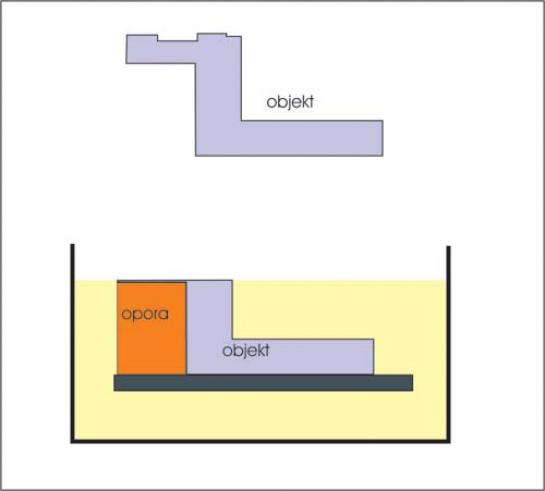
Čas izdelave je odvisen od velikosti in zahtevnosti objekta. V povprečju se ena plast strdi v eni ali dveh minutah, kar pomeni, da tipičen proces izdelave traja 6 do 12 ur. Po zaključku izdelave mora objet še v »ultravijolično« pečico, kjer plastika doseže svojo zahtevano trdnost. Po tej fazi je proces izdelave dokončan, po potrebi lahko objekt še dodatno površinsko obdelamo (brušenje, barvanje).
Poudarki tehnologije SLA:
• Prva in najbolj množično uporabljena tehnologija hitre izdelave objektov (prototipov).
• Kljub za običajne smrtnike visoki ceni naprav in surovin, so te nižje od cen drugih tehnologij, z izjemo najnovejše tehnologije brizganja.
• Uporablja na svetlobo občutljivo tekočo plastično maso (surovina, iz katere »nastane« objekt).
• Zahteva dodatno površinsko obdelavo, saj laser sam po sebi ne zagotovi dovolj gladke površine. S tem so lahko težave, saj preveč »brušenja« lahko vpliva na kompaktnost (strukturno trdnost) objekta.
• Izdelani objekti so krhki (drobljivi), uporaba tekoče plastike v procesu izdelave pa povzroči, da je površina objekta na dotik lepljiva.
• Prehodi med plastmi so dokaj izraziti (zaradi tega zahteva brušenja). Predvsem je to lahko problem na osi z – v smeri od spodaj navzgor, kot nastaja objekt (stopničast prehod med plastmi).
• Pri izdelavi nekaterih objektov jih je treba med izdelavo dodatno podpreti.
• Surovina (tekoča plastika) je lahko strupena in zdravju škodljiva.
SELECTIVE LASER SINTERING (SLS)
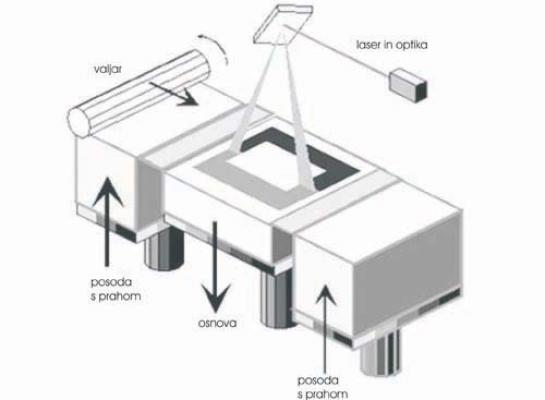
Tehnologija SLS je nadgradila tehnologijo SLA, tako da omogoča večjo svobodo pri izbiri materialov. Ti so v obliki finega prahu, ki ga laserski žarek stali. Ne gre torej za strjevanje na svetlobo občutljivih materialov, temveč za toplotno obdelavo. Da pa to ne bi zahtevalo močnega izvora laserja (tipično 50 W CO2 laser), je prah v procesu izdelave segret na temperaturo malo pod tališčem. Zaradi uporabe prahu je proces izdelave objekta nekoliko drugačen. Napravo sestavljajo dve posodi s prahom in transportni mehanizem. Ta prah (surovino) prenese na delovno površino, kjer stali površino, ki je del objekta. Delovna površina se spusti za debelino ene plasti in proces se ponovi, to pot iz druge smeri. In tako naprej, dokler objekt ni izdelan. Proces izdelave poteka znotraj nadzorovanega okolja, običajno dušikove komore, kar prepreči oksidacijo materiala (v skrajnem primeru celo eksplozijo).
Površina s tehnologijo SLS izdelanega izdelka je veliko bolj porozna (luknjičasta) kot površina objekta, narejenega s tehnologijo SLA – kar ima svoje prednosti in slabosti. Temu je tako zaradi dejstva, da se delci materiala med seboj povežejo (delci prahu) zaradi delnega in nepopolnega taljenja materiala. Tehnologija zahteva dober nadzor nad temperaturo – moč laserja, saj lahko previsoka temperatura povzroči nepravilno strjevanje (ali celo prelivanje stopljenega materiala) in s tem nepravilno izdelan objekt. Tehnologija SLS ima prednost v tem, da običajno ne zahteva dodatne podpore za nekatere oblike objektov, saj to zagotavlja preostali, nestaljeni prah na delovni površini.
Poudarki tehnologije SLS:ž
• Zaradi uporabe drugih surovin je lahko objekt konstrukcijsko močnejši – to pomeni, da je moč izdelati tudi objekte, ki jih s tehnologijo SLA ni mogoče.
• Laser topi surovino, ki je v stanju finega prahu – na voljo je več različnih materialov (plastika, vosek), ne pa zgolj en sam, kot pri tehnologiji SLA.
• Tudi tu se lahko pojavi problem v »stopničasti« površini objekta.
• Površina objekta je po izdelavi »luknjičasta« (porozna) zato je tudi v tem primeru priporočljiva površinska obdelava. Brušenje je zaradi tega preprostejše, preprosto je tudi odpraviti napake, nastale med procesom izdelave. Če pa želite imeti gladko površino, je treba na objekt naknadno nanesti površinsko snov (tesnilno maso), ki zapolni luknjice. Ta še dodatno utrdi objekt.
LAMINAR OBJECT MANUFACTURE (LOM)
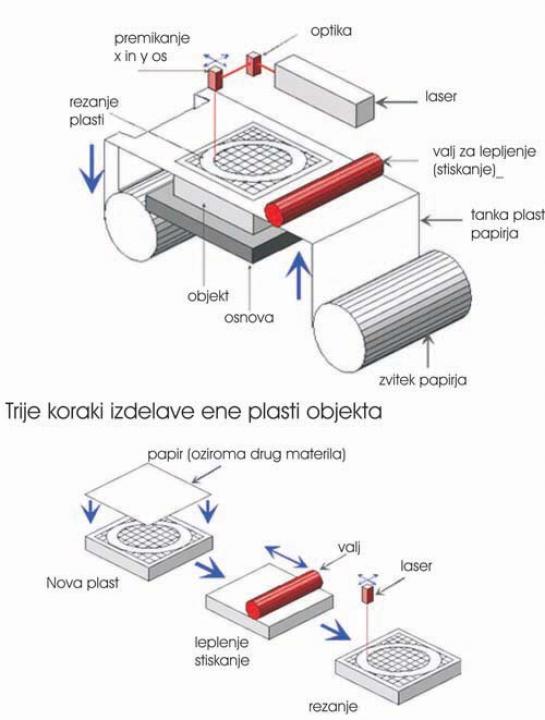
Še več svobode pri izboru različnih materialov ponuja tehnologija LOM (papir, plastika, kovina). Načelo izdelave je tudi pri tej tehnologiji podobno: objekt sestavljajo posamezne plasti, pri čemer je njihova debelina odvisna od materiala in moči laserja. Tanjši kot je material, manj moči potrebujemo, da iz površine materiala, ki je na voljo, izrežemo posamezne plasti.
Tipično napravo sestavlja »zvitek« ali pole materiala (običajno papir), ki ga mehanizem premika preko delovne površine. Na spodnji površini plasti je naneseno lepilo, ki povzroči, da se plasti med seboj zlepijo. Laserski žarek »izreže« plast, delovna površina se spusti za debelino materiala, nato pa iz zvitka »potegne« novo plast. V tej fazi naprava stisne plasti, da se te med seboj zlepijo. In tako naprej, dokler objekt ni narejen. Tudi v tem primeru odvečen material pomaga pri trdnosti objekta v fazi izdelave.
Ko so prvič predstavili tehnologijo LOM, so uporabljali zgolj papir, kar povzroča, da izdelan objekt ni dovolj trden. V primerih, ko izdelujemo zgolj maketo bodočega izdelka, to načeloma ni problem. Če pa izdelujemo kaj bolj konkretno uporabnega, je treba poseči po drugih materialih. Na primer po plastiki ali kovini. Treba pa je omeniti, da tehnologija LOM ni močno razširjena in verjetno zaradi novih tehnologij brizganja tudi v bodoče ne bo.
Poudarki tehnologije LOM:
• Model je sestavljen iz zlepljenih plasti, izrezanih z laserjem.
• Prednost tehnologije LOM je nizka cena materiala.
• Ker pri izdelavi objekta ne potekajo kemične reakcije, so objekti lahko večji od tistih, izdelanih po tehnologiji SLA ali SLS.
• Tudi tu utegne biti težava »stopničasta« površina objekta. To zahteva dodatno površinsko obdelavo, katere težavnost oziroma možnost je odvisna od izbora materiala.
• Izdelani model je treba zaščititi pred vlago, še posebej ko gre za objekt, izdelan iz papirja.
FUSION DEPOSITION MODELING (FDM)
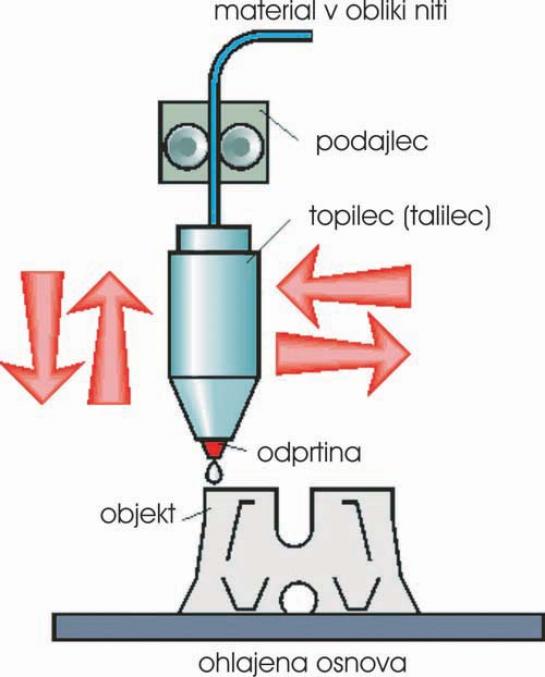
Tehnologija FDM je nekakšna predhodnica tehnologije brizganja, ki se pojavlja v zadnjem času. Preprosto povedano gre za to, da se material (plastika, vosek) v »šobi« zaradi temperature stali. Šoba, ki se premika v dvodimenzionalni ravnini, nato nanese tanko plast na delovno površino, nakar se ta nekoliko premakne navzdol in proces se tudi v tem primeru ponavlja, dokler objekt ni izdelan. Za izdelavo nekaterih objektov (podobno kot pri tehnologiji SLA) je treba zagotoviti podporo med postopkom izdelave. Osnovna prednost tehnologije je dokaj enostaven postopek, ki vključuje laser in dopušča dokaj velik izbor različnih materialov.
Komora, v kateri poteka izdelava objekta, je segreta na temperaturo malo pod tališčem materiala, kar olajša njegovo taljenje znotraj »šobe«. Delovna površina, na kateri nastaja objekt, in on sam pa sta lahko ohlajena, kar pohitri proces, saj se plast tako hitreje strdi, kar zmanjša potreben čas za izdelavo objekta.
Poudarki tehnologije FDM:
• Možno je uporabiti materiale (termoplastika ABS), ki dopuščajo izdelavo strukturno funkcionalnih objektov.
• Pri izdelavi objekta je moč uporabiti dva različna materiala.
• Tudi tu utegne biti težava »stopničasta« površina objekta. To zahteva dodatno površinsko obdelavo, katere težavnost oziroma možnost je odvisna od izbora materiala.
• Mogoče je izdelati dokaj velike objekte (60 x 60 x 50 cm)
• Segreto plastiko, ki tvori posamezne plasti, stisnejo tako kot zobno pasto iz tube. Ta se hitro strdi, saj je delovna površina ohlajena.
SOLID GROUND CURING (SGC)

Gre za zanimivo tehnologijo, ki je nekakšna izpeljanka tehnologije SLA, torej tudi ta uporablja na svetlobo občutljiv material, hkrati pa zagotavlja veliko hitrejšo izdelavo objekta. To dosežejo tako, da naprava celotno plast izdela skoraj trenutno, torej odpade čas, potreben za to, da laserski žarek osvetli površino, ki tvori plast objekta, kot je to pri tehnologiji SLA.
V prvem koraku izdelave posamezne plasti, delovno površino (ploščo) poškropijo s tanko plastjo na svetlobo občutljive smole. Za vsako plast v naslednjem koraku izdelajo masko (s tehnologijo ionografskega tiskanja), ki jo namestijo nad delovno ploščo. Tam, kjer želimo, da se smola strdi, so na maski odprtine, prek katere na smolo »pade« UV-svetloba. V tretjem koraku zadevo osvetlijo z UV-lučmi. Ko se »obsevana« smola strdi, masko umaknejo in s sesalnikom izsesajo nestrjeno smolo, ki gre nazaj v proces. Plast (oziroma objekt) gre še enkrat pod UV-luč, ki plast dodatno utrdi in utrdi tudi tiste ostanke smole, ki jih sesalnik ni uspel izsesati. Nastale »luknje« zapolnijo z voskom, ki zagotavlja podporo v procesu nastajanja objekta in hkrati zagotovi osnovo za nanašanje naslednje plasti. V zadnji fazi pred nanašanjem naslednje plasti površino zbrusijo, kar vpliva na večjo kakovost objekta. Proces ponavljajo, dokler objekt ni izdelan, nakar le še odstranijo vosek, v katerem so tudi ostanki smole.
Poudarki tehnologije SGC:
• Mogoče je hitro izdelati velike objekte (50 x 50 x 35 cm)
• Velika hitrost izdelave omogoča hitro sočasno izdelavo več malih objektov ali enega velikega.
• Za vsako plast izdelajo masko, kar omogoča izdelavo celotne površine plasti naenkrat, hkrati pa je zaradi dodatne uporabe voska nepotrebna dodatna podpora pri izdelavi nekaterih objektov.
• Zagotovljena je dovolj kakovostna površinska obdelava, tako da dodatna obdelava objekta običajno ni potrebna.
BRIZGANJE V TREH RAZSEŽNOSTIH
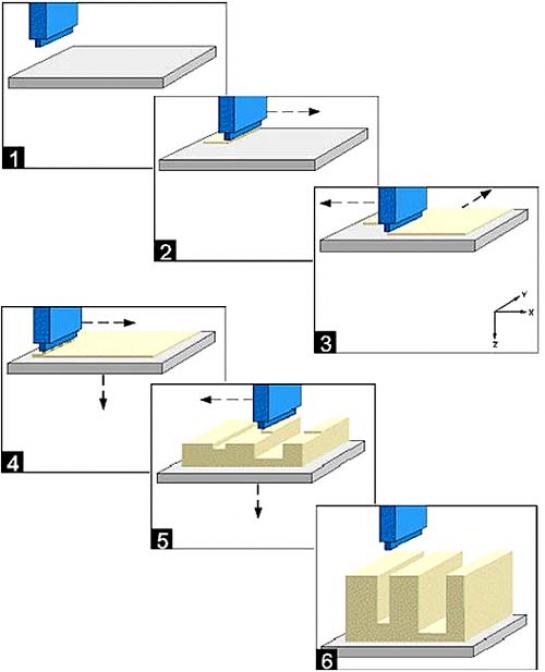
Osnova tehnologije so brizgalni tiskalniki, ki jih poznamo iz običajnega sveta računalnikov. Tako kot pri drugih tehnologijah, tudi pri tej nastaja objekt plast za plastjo, le da so te plasti veliko tanjše in je torej končni rezultat večja kakovost objekta. Hkrati lahko tekoči plastiki, ki jih tiskalna glava nanaša na delovno površino in tako tvori objekt, dodamo barvilo in tako dobimo barvni objekt. V tiskalniški glavi je več šob, zato je izdelava posamezne plasti lahko hitrejša ali v primerih različnih barv tudi barvna. Tudi v tem primeru, morda zaradi tanke plasti še toliko bolj, je pri nekaterih oblikah objekta treba zagotoviti podporo v posameznih fazah izdelave objekta
3D-tiskanje pomeni korak najprej med tehnologijami hitre izdelave prototipov. Naprave so manjše, manj zahtevne za vzdrževanje in cenejše. S tem so cenejši tudi objekti, ki jih tako naredimo, in zato so toliko dostopnejše širšemu krogu uporabnikov.
Tudi pri napravah za 3D-tiskanje gre za enak postopek izgradnje objekta. V praksi to pomeni, da ta nastaja plast za plastjo, razlikujejo pa se po kakovosti uporabljenih materialov in ne nazadnje tudi debelini plasti. Zanimivo pa je, da tudi pri teh napravah ne gre zgolj za eno tehnologijo, temveč za več različnih. Pravilno povedano je brizganje, kot ga poznamo iz sveta brizgalnih tiskalnikov, zgolj en postopek.
Sistem Perfactory posamezne plasti naredi iz materiala, občutljivega na svetlobo. Tega stisne pod stekleno ploščo, na katero projektor projicira »masko« (podobno kot pri tehnologiji SGC). Osvetljene površine se strdijo, druge ne in tako nastane ena plast objekta. Kot material sistem uporablja akrilat (acrylics), epoksi smole in nekatere biološko združljive materiale, pri čemer so lahko objekti prozorni, rdeči ali modri. Objekt pri tem sistemu raste v višino s hitrostjo 2,54 centimetra (en palec) na uro.
Za drugačno tehnologijo se je odločilo podjetje Z Corp. Ta že uporablja tehnologijo brizgalnih tiskalnikov, a ne z neposrednim brizganjem materiala, iz katerega je zgrajen objekt. Namesto tega naprava brizga majhne kapljice lepila na plast finega prahu (plastika). Kjer je lepilo, se delci prahu zlepijo, drugod pa ne, in tako plast za plastjo nastane objekt. Lepilo je lahko obarvano, kar pomeni, da je možno izdelati objekte različnih barv. Zaradi svojevrstne tehnike in uporabljenih materialov, so lahko izdelki, narejeni s temi napravami, strukturno čvrsti in imajo različne lastnosti. Objekt pri tem sistemu raste v višino s hitrostjo med 2,54 in 5 centimetrov na uro.
Podjetje 3D System pa že uporablja neke vrste klasično brizgalno tehnologijo, imenovano multi jet modeling. Tu glava (oziroma šobe v njej) neposredno brizgajo majhne kapljice materiala na delovno površino in tako plast za plastjo gradijo objekt. Podobno velja tudi za nekatere druge naprave tega podjetja, ki pa kot material uporabljajo stopljeni vosek. Poleg voska uporabljajo še akrilat, ki je lahko različnih barv. So pa te naprave najpočasnejše, saj je čas nastajanja objekta pet- do desetkrat daljši od časa izdelave pri, na primer, napravah podjetja Z Corp.
Obstaja tudi razmeroma cenen izdelek, ki tako spada pod to kategorijo naprav, ki uporablja tehnologijo FDM (Fusion Deposition Modeling). Dejali smo že, da gre pri tem za »stiskanje« oz. nanašanje stopljene plastike skozi šobo. Sistem podjetja Dimension kot material uporablja plastiko ABS. Po hitrosti izdelave objektov pri teh (cenenih) napravah ne gre za bistveno odstopanje. Čas izdelave je odvisen od velikosti objekta, ki ga želimo narediti. Če je ta tak, da ga je moč držati v dlani, bo naprava zanj porabila dve uri. Za večjega pa pač nekoliko več.